The Building Materials Shortage of 2021
The Building materials shortage and what we are doing to make sure our customers never need to be concerned about it.
In June of 2021, the IHS/Markit CIPS survey highlighted that 77% of firms within the construction industry reported longer lead times from suppliers, while prices for products and raw materials rose at their fastest rate since the survey was launched.
With a push from the government to ‘build back better, the construction industry is faced with the mammoth task of delivering better commercial infrastructure, improving public transport and building better homes whilst managing a building materials shortage.
With the combination of Covid-19, Brexit and the intense boom in demand across the construction industry in the past year, at Key Integrated Services we have witnessed increasing building materials shortages as well as a significant increase in material prices.
With 2020 bringing the sharpest rise in commercial work since September 2014 (according to the IHS Markit/CIPS UK Construction Total Activity Index), demand has strengthened, global supply chains have been stretched and commodity prices have risen. Here are our thoughts on the current status of the construction industry supply chain.
What is the cause of the building materials shortage?
Brexit
The departure of the UK from the EU in the early months of 2021 inevitably meant changes to customs rules as a direct result of Brexit, which slowed imports of building materials, as well as other goods, due to border forces having to deal with new and lengthy bureaucratic paperwork between the EU and the UK. As a result, this put greater pressure on building material prices and created a shortage.
A complex supply chain situation
Another pertinent factor is of course the coronavirus pandemic. Covid-19 has obviously played its part in causing restrictions on movement and commerce across the world. It has put incredible pressure on the entire logistics industry, impacting the movement of freight which in turn has led to a surge in the cost of building products shipped in containers. However, it’s not just the pandemic that has had a significant effect on the building materials supply chain. An increase in demand for particular materials, such as steel, has naturally resulted in shortages, order backlogs and a sharp rise in prices. The steel shortage was initially a result of pandemic-induced production cuts back in March 2020, however, with the unexpected automotive demand of late 2020, steel mills have struggled to accommodate the demand. Their mills are no longer able to adjust their production to the current demand, leading to a shortage internationally.
Timber prices in particular are also likely to continue to increase across 2021. Communications from the Timber Trade Federation and their partners in Sweden, who supply almost 50% of the structural timber that is used in the UK, have warned that their stock levels are at their lowest in 20 years. Moreover, most wood arriving in the UK has already been pre-sold to customers and despite strict allocations of materials, most buyers are unable to buy the timber they need for their business.
How do you overcome a materials shortage?
Here at KeyIS, whilst we have noticed a significant price increase in a very short space of time, we haven’t experienced many instances where we couldn’t source the materials we needed. We were, however, put in a position where we were going to have to reduce the validity periods of our tender to four weeks which was not a viable option for the livelihoods of our customers. This is how we dealt with the material shortage.
- We initially negotiated with our suppliers to ensure a fixed the prices for us, leveraging our strong relationships.
- As a result of increased lead times from eight weeks to twenty weeks, we had to ensure early engagement with our customers. Our focus had to shift to ensure that we designed larger products (such as air handling units and chillers) first so we could order these items of plant in good time.
- We enhanced our management processes across client communication, process management and supplier relationships to ensure that projects were delivered on time, despite the shortages and increased lead times.
Since January 2021, we have successfully completed over 440 maintenance jobs and over 160 projects. Thus, overall we feel that despite the national material shortages, which have evolved from a direct boost in the economy after the successful stimulus programme, we have adapted effectively ensuring that changes to the supply chain have not negatively affected our business or the expectations of our customers.
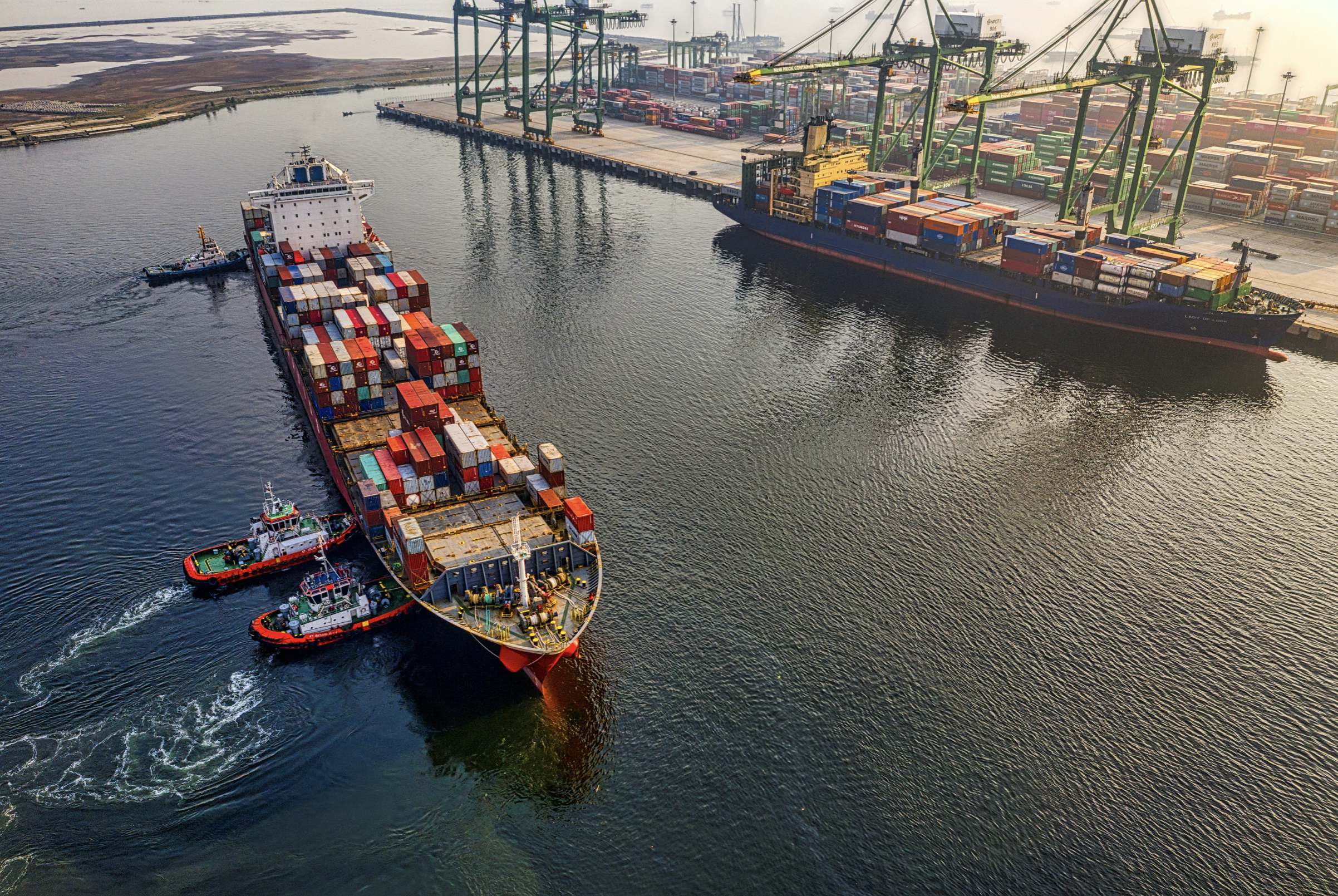